Blog
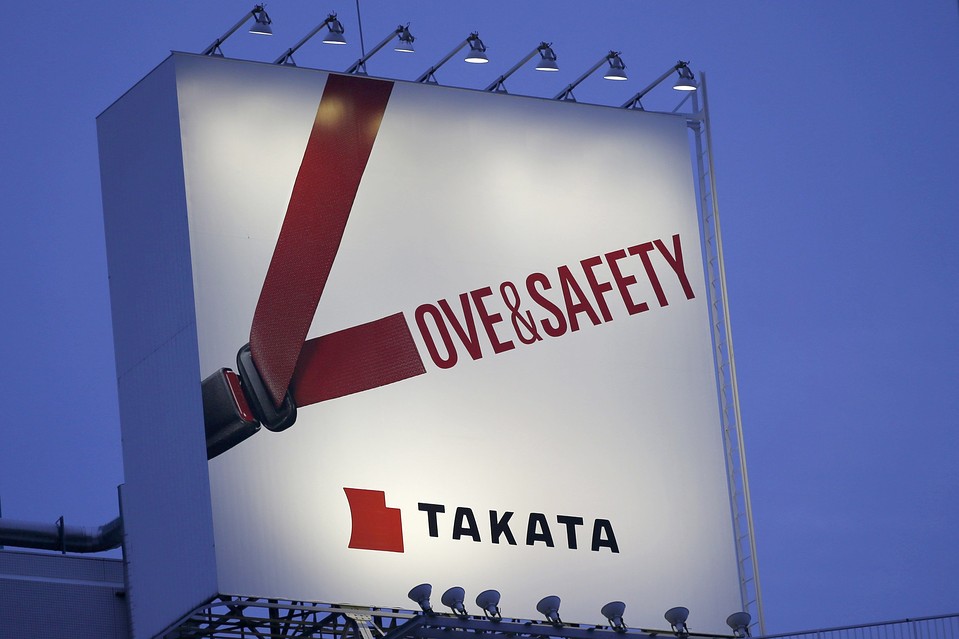
Auto Industry Convenes Meeting to Determine What Caused Air-Bag Failures
A billboard advertisement for air bag and seat belt maker Takata Corp. in Tokyo last year. REUTERS
By YOKO KUBOTA
Jan. 13, 2015 6:11 p.m. ET
DETROIT—Car parts suppliers are stepping up quality control efforts and the traceability of their components in the wake of an unprecedented wave of auto-safety recalls and massive fines against manufacturers.
Several are investing in new equipment to better automate defect-detection and assigning more employees to parts checks. Daicel Corp. , which makes air bag inflaters, the explosive devices that pump up an air bag in event of a collision, has invested several million dollars to beef up its system for tracking inflaters shipped to customers, a spokesman said.
It acquired capable of carving letters data onto tiny metal parts, such as when and where the parts were made. Previously, Daicel attached bar codes to many parts, but some pieces were too small to do so.
“It’s not anything dramatic and it costs us money, but it’s important that we can immediately identify the range of potentially problematic products should an issue arise. Otherwise the problem could expand and we may have to use a lot of manpower to specify the range,” the spokesman said.
Aisin Seiki Co. , the world’s fifth biggest automotive supplier by revenue, analysts said, is spending tens of millions of dollars to boost quality. It traditionally relied on experienced employees to detect and fix blow holes, or small pores, that occur in aluminum die casting. It bought new devices that catch such problems, and cut the defect rate by two-thirds, said Fumio Fujimori, the company’s president.
Posted on January 2015,16 // Author: Admin